Passivhaus
A STEP-BY-STEP GUIDE TO DESIGNING TO PASSIVHAUS STANDARDS
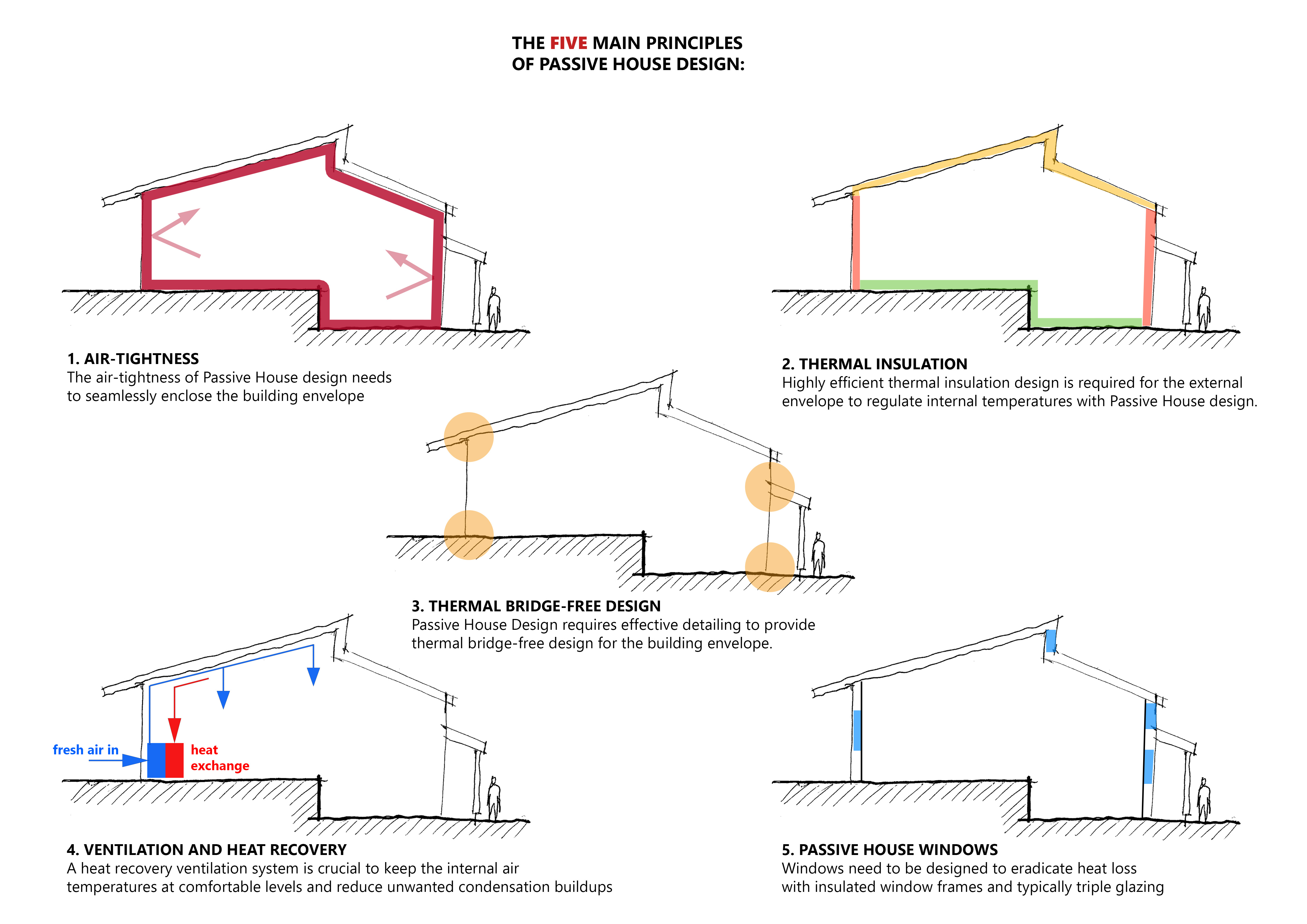
When designing to Passivhaus Standards there are several significant factors Architects need to consider when discussing a new project for their clients. These factors help define key elements of a project in the initial design phases, ensuring that early concept planning is followed as guided by industry approved standards and methodologies.
Before starting the project, it’s important to consider which Passivhaus class the building is intended to reach. There are three main classes:
1. Passivhaus Classic: The traditional Passivhaus
2. Passivhaus Plus: Includes additional energy generated, such as solar PVs.
3. Passivhaus Premium: More energy is produced with a high renewable primary energy demand factor requirement.
There are several Passivhaus standards one would need to consider when seeking to achieve Passivhaus certification. This article will focus on 6No. Steps to start your journey in Passivhaus project design and development,
Step1 - SHAPE; Step2 - ENVELOPE; Step3 - WINDOWS; Step4 -VENTILATION; Step5 - HEATING & Step6 - CERTIFICATION.
One of the most important factors which needs to be considered as part of the initial design process is the shape/form of the overall building design. This is because one of the primary Passivhaus standards is based on what is referred to as the HEAT LOSS FORM FACTOR (HLFF).
This is a calculation where the sum total area of the exposed thermal envelope (walls, soffits, ceilings and roofs) is determined against the treated floor area, which are the rooms within the building which are heated. This excludes areas of internal partitions, doors, stairs and unusable spaces.
HLFF = HEAT LOSS AREA / TREATED FLOOR AREA.
There is the requirement to consider the thermal performance of the building envelope early on by following these requirements.
+ Ensure that excellent airtightness is designed in.
+ Aim for no structure or service penetrations of the airtight layer.
+ Design for thick & continuous thermal Bridge free design.
+ Quality is more than quantity.
+ Be aware that gap and air leakage can greatly reduce the benefit of thick or low conductivity insulation.
Window design and specification is a critical component of Passivhaus design.
+ For a building to be Passivhaus certified, it is likely that triple-glazing will be a key consideration.
+ Window placement on elevations and window-to-wall ratio are two significant design considerations.
+ Occupants receive purified, filtered air with outstanding results.
+ Comfort ventilation with heat recovery is required for most heating and cooling climates.
+ Early consideration results in cost savings due to minimised duct length and number. This helps optimise ventilation rates.
+ Ventilation systems must be of high quality with correct filters and attenuation.
+ It is recommended to ONLY use Passive House Certified Units as the certification includes the testing of noise and internal air leakage. Also allows for a more realistic measure of actual heat loss compared with other criteria.
+ It is important to consider the design specifications of the mechanical heating and heat exchangers early on in the design phase.
It is recommended to contact a Passive House certifier at an early stage of the planning phase as any problems can be remedied. The certification Process consists of 5 phases:
1. Initial check – When? At the start of a project:
- To check whether project contains special aspects and how they should be assessed in the building certification.
2. Preliminary Review – When? During the design phase:
- Assessment of the concepts for the design, insulation and building services
- The preliminary version of the PHPP calculation.
- Wise to apply to large projects.
3. Design Stage Review – When? Before the start of the construction work:
- Energy relevant planning documents
- Technical data of construction products
- Preliminary version of the PHPP calculation required
4. Queries regarding certification – When? Continually during planning and construction:
- For planning decisions which affect the energy balance coordinate with the certifier at an early stage.
5. Final Review– When? After completion of the constriction work:
- Any change to the planning drawings needs to be updated for the final review.
- Proof of the execution of the work.
At Lytle Associates Architects, we are an award-winning practice, with extensive knowledge in architectural design across a range of sectors, with over 35 years of experience in the built environment.
We have the privilege of obtaining in-house, certified Passivhaus designers, therefore allowing us to apply accurate energy and fabric-first modelling, in the early stages of the design process for your building. This helps ensure that a homogenous, healthy and energy efficient design output is achieved. We would be happy to assist you where we can, in achieving this gold standard in the sustainable design of your building.
Please feel free to contact me directly at 01483 301661, or via email at prawsthorn@lytle-associates.com.